Pike Corp. aims to reduce the cost of tool replacement and ensure the right tools are on the right work site”Tracks Tools with RFID”, thanks to an automated RFID- and GPS-based system from Silent Partner Technologies.
When electric utility vehicles travel to construction or maintenance sites, they carry thousands of dollars’ worth of tools, and the tracking of those items can be a challenging distraction for the crews assigned to build and repair power lines. Pike Corp., which provides construction, repair and engineering services for power lines and substations across the United States, uses RFID technology to ensure all trucks are properly stocked, as well as to view tool usage and prevent shrinkage. The RFID Tool Tracker solution, provided by Silent Partner Technologies (SPT), is being installed in vehicles by equipment supplier Altec.
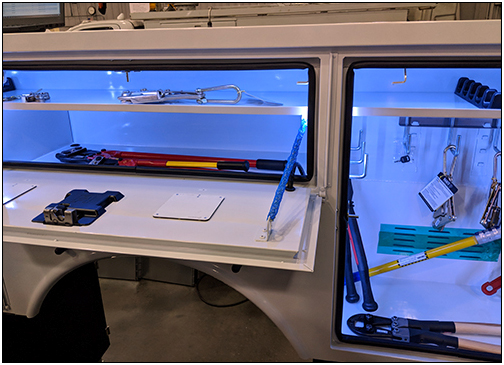
Pike Corp. is a national utility electric contractor with thousands of employees and thousands of utility vehicles—with a total of hundreds of thousands of tools loaded onto them—and serves more than 300 investor-owned utilities. The firm builds new power lines, as well as maintaining existing ones, using crews and trucks deployed all over the United States. “Our challenge was finding a way to manage the tools on those vehicles,” says Cliff Edwards, Pike Corp.’s special projects VP, in order to minimize loss and increase efficiency in the tracking of tools. “Our job is to safely build power lines while being productive,” he says, and manually tracking assets took time away from that critical effort, both for management at company headquarters and for crew at work sites. Typically, when a loaded utility truck leaves Pike Corp. for a customer’s site, it may not return for years. The vehicle will serve the construction needs at one location, and often then be sent to another site in a neighboring area. Therefore, tracking what is on the vehicle, as well as its condition, required some manual effort for tool counting and the inputting of data into a database. If workers found that a new tool was needed, they would then place a request for that item.
Losing track of even one or two tools can be costly, and the company may end up replacing tools that have merely been misplaced—for instance, they might merely be on another vehicle. Additionally, there’s the matter of ensuring that all tools are available when they’re needed. One utility company may require different sized tools than another, so it’s important for the dispatcher to understand what is aboard each vehicle, as well as whether it will meet the requirements of a specific project.
Pike Corp. sought a solution that wouldn’t require any effort from its field personnel. “We had the idea that knowing what inventory is on a vehicle should be automated,” Edwards says. That meant a hands-free system that would not require handheld scanners. The company experimented with a variety of technologies, then began working with SPT on a UHF RFID- and GPS-based solution in early 2017. Altec, which supplies many of the tools used by Pike’s crews, is installing the RFID readers and antennas on the utility trucks. It is also applying UHF RFID tags to tools that it sells to the utility service company.
Pike Corp. and Silent Partner Technologies experimented with a fixed solution that would track what goods are on any given vehicle. By reading RFID tags on each piece of equipment in real time a reader with 32 antennas on the vehicle provided that level of granularity. However, says Will Crouch, a Pike financial analyst, that was more than what was needed, and the installation costs would be exorbitantly high.
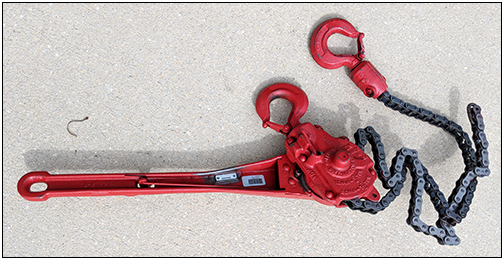
Ted Kostis, Silent Partner Technologies president, says the team instead installed a system with only nine antennas, which could capture the passing of tagged items into and out of the vehicle. The antennas also read tags inside the truck, without knowing specifically where within the vehicle they were located.
First, each product—such as a chainsaw, a cable cutter or some other piece of equipment—has a UHF RFID tag attached to it. The unique ID number encoded on the tag is linked in the Silent Partner Technologies software (residing on Pike’s server) to data about that tool, such as its manufacturer, when it was put into service and when it was inspected or repaired. The system also captures GPS data, which is then linked to the read data so that the software can determine at which site those tools were removed or returned.
A Silent Partner Technologies AP1000 reader is powered by the vehicle’s engine, so it transmits data back to the server via a cellular connection, only if the vehicle engine is running (which is typically the case during the loading and unloading processes). The system can then be set to send data at specific intervals, such as every 15 minutes, when the engine is running, as well as when the ignition is turned on.
Crouch says one of the project’s challenges was to ensure that all pieces of equipment on a variety of materials, could be easily read within each truck and as they were loaded or unloaded. That meant using multiple types of tags to ensure that those on fiberglass, plastic, metal or a combination of materials could be properly read. The tags were applied using epoxy that was tested to make sure the rigors of the environment in which the tools would be used wouldn’t damage the tags or knock them loose.
Several hundred tools were initially tagged and tracked in California, North Carolina and Florida. The company’s management can now view each vehicle’s location and determine what tools are loaded onto it, as well as where tools were removed and then returned (indicating they were used for construction work). “We’re able to see tools on any given truck,” Edwards state, “as well as movement from one truck to another.”
The company has approximately 50 vehicles deployed with RFID technology to date, enabling it to track the use of assets at customer sites. “Our goal is to have the system bulletproof before going out to do the rest of the trucks,” Edwards explains—of which there are thousands.
The data not only ensures that the company knows what tools are loaded onto each vehicle, but also enables analytics. Workers, for instance, can view how often tools are used, as well as which tools are rarely or never used. In that way, the company can better strategize the stocking of each vehicle to meet the demands of most projects, adding more of commonly used tools, and fewer (or none) of those that haven’t proven to ever leave the vehicle. The system also could be used in the future to offer an alerting functionality, in order to let management or drivers know if a tool is being left behind on a client site.